Ihr kompetenter Partner
Als Abteilung „Fügetechnik und Additive Fertigung“ sehen wir das Füge- und Schweißverfahren sowie die Additive Fertigung als Dreiklang aus Prozesstechnik, Werkstoffzustand und den resultierenden Festigkeitseigenschaften. In experimentellen Untersuchungen und numerischen Prozesssimulationen prüfen wir den Einfluss der Prozessparameter auf das entstehende Gefüge, die Ausbildung der Geometrie und der mechanischen Eigenschaften. Unser Portfolio beinhaltet auch verschiedene Methoden der experimentellen Spannungsanalyse, um Eigenspannungen im Labor und vor Ort zu ermitteln.
In den Bereichen Fügetechnik, Additive Fertigung, Wasserstoff und ZfP erwarten Sie bei uns viele spannende Projekte. In einem stetig wachsenden Team aus Doktorandinnen und Doktoranden forschen Sie an hochaktuellen Herausforderungen von Energiewende, E-Mobilität, Fahrzeugleichtbau, Wasserstofftransport und CO2-Reduktion.
Bei Interesse an einer Promotion und unseren Projekten freuen wir uns auf Ihre Initiativbewerbung unter Bewerbung@mpa.uni-stuttgart.de
Die Referate der Abteilung Fügetechnik und Additive Fertigung
-
Additive Fertigung
Das Team „Additive Fertigung“ an der MPA forscht im Bereich hochbeanspruchter metallischer Bauteile mittels Laser-Pulverbett-Schmelzen (PBF-LB/M) und Lichtbogen-Draht-Fertigung (WAAM). Das Prozess-Know-How der MPA und die zur Verfügung stehenden Anlagen und Simulationsmethoden werden dabei in Forschung, Lehre und Auftragsfertigung eingesetzt. Dabei verfügt die MPA über Kompetenzen in der gesamten additiven Prozesskette. Diese beginnt bei der Bauteilkonstruktion, Anlagenvorbereitung und geht über den Anlagen-Betrieb, die Nutzung von Prozessmonitoring bis hin zur Bauteilentnahme und Nachbearbeitung.
Hier finden Sie weitere Informationen zu unserem Team und den Anlagen des AM-Labors.
-
Fügeverfahren
Das Referat Fügeverfahren forscht an verfahrenstechnischen, fertigungstechnischen und metallurgischen Fragestellungen der Schweißtechnik. Schwerpunkt ist das Rührreibschweißen und das Widerstandspunktschweißen höherfester Aluminium- und Stahllegierungen. Zudem können in unseren Laboren das Buckelschweißen und Ultraschallschweißen sowie Schmelzschweißverfahren untersucht werden. Wir bieten experimentelle Arbeiten wie Parameterstudien, Prozessoptimierung sowie Untersuchungen zu Wärmebehandlungen, entstehenden Gefügen und der resultierenden Festigkeitseigenschaften an.
-
Spannungsanalyse und Eigenspannungen
Mit verschiedenen Methoden experimenteller Spannungsanalyse können wir Eigenspannungen an Schweißverbindungen und Großbauteilen sowie Beanspruchungen beim Betrieb eines Bauteils oder einer Komponente ermitteln. Zu unseren Kompetenzen zählen Messung von Eigenspannungen, Optische Dehnungsmessung sowie Applizieren von Dehnungsmessstreifen und Ausbilden von Bauteilen zu Kraftmessgliedern. Neben Untersuchungen in unserem akkreditierten Labor führen wir Messungen von Eigenspannungen, Kräften, Dehnungen, Verformungen und Verschiebungen auch beim Kunden vor Ort durch.
Transformation-Hub Cyber Join
Das Referat und damit der Transformations-Hub CyberJoin unterstützt Fahrzeughersteller und Zulieferer im Automobilsektor, insbesondere bei der Integration alternativer Antriebskonzepte und dem Leichtbau. Er fördert den Wissenstransfer und bündelt Trends aus Forschung und Entwicklung, um technologische und wirtschaftliche Herausforderungen anzugehen. CyberJoin bietet eine virtuelle Forschungsplattform, Website sowie regelmäßige Wissenstransfer-Veranstaltungen wie Workshops und Messen an. Ziel ist es, die Zusammenarbeit zwischen Wissenschaft, Industrie, Zulieferern und Fahrzeugherstellern zu stärken und ein Innovationsnetzwerk aufzubauen. Die Materialprüfungsanstalt Universität Stuttgart und die Gesellschaft für Schweißtechnik International mbH leiten gemeinsam die Aktivitäten des Hubs und organisieren bundesweite Netzwerktreffen an sieben Standorten.
Aufgaben und fachliche Schwerpunkte
Unsere Abteilung bietet ein umfassendes Spektrum an Dienstleistungen und Prüfungen. Informieren Sie sich hier über die von uns angebotenen Leistungen oder kontaktieren Sie uns telefonisch oder per E-Mail
- Durchführen von Musterschweißungen
- Fügetechnische Beratung
- Vor Ort-Support, Nachstellen von Prozessproblemen im Labor und Fehleranalyse
- Messen von Prozessgrößen, z. B. Strom, Spannung, Kraft, Verschiebung, Temperatur etc.
- Messen von Übergangswiderständen und elektrischen Stoffwiderständen
- Messung von Eigenspannungen
- Applizieren von Dehnungsmessstreifen und Ausbilden von Bauteilen zu Kraftmessgliedern
- Optische Dehnungsmessung
- Numerische Prozesssimulation (FEM) im Bereich der Schweißtechnik - Physikalische Simulation von schweißtypischer Gefügeausbildung
- Prüfungen an geschweißten Proben (ZfP, Festigkeit, Metallographie)
Wir forschen im Bereich der Additiven Fertigung sowie der Fügetechnik und entwickeln Lösungen zu aktuellen Fragestellungen.
- Kontinuumsmechanische, multiphysikalische Simulation von Fügeverfahren. Insbesondere Widerstandpunktschweißen, Rührreibschweißen, Fließlochbohren etc.
- Entwicklung numerischer Simulationsmethoden für die additive Fertigung mittels selektivem Laserstrahlschmelzen
- Entwicklung neuer Verfahrensabwandlungen für Aluminium-Stahl-Verbindungen
- Untersuchung der Wechselwirkung von Fügeverfahren und Wärmebehandlung
- Untersuchung und Bewertung additiv gefertigter Proben und Bauteile
- Entwicklung neuer Fügekonfigurationen für Mischverbindungen
- Entwicklung von Werkstoffmodellen für die Simulation von Schweißprozessen
- Entwicklung von neuen Verfahren zur Bestimmung von Eigenspannungen
- Entwicklung von Kraftaufnehmern für besondere Einsatzbedingungen
Um unserer gesellschaftlichen Verantwortung gerecht zu werden, beteiligen wir uns aktiv an Fachausschüssen, Gremien und Kommittees und bringen so als unabhängige Stelle wichtige Erkenntnisse aus Forschung, Entwicklung und Anwendung in Richtlinien und Normen ein.
- DVS Fachausschuss 5 „Sonderschweißverfahren“
- DVS Fachausschuss 4 „Widerstandsschweißen“
- DVS Arbeitsgruppe V11.2 „Rührreibschweißen“
- DVS Arbeitsgruppe V3.2 „Punkt-, Buckel- und Rollnahtschweißen“
- VDI/VDE-GMA FA 2.11 „Elektr. Messverfahren; DMS-Messtechnik“
- AWT FA13 „Eigenspannungen“
- Rührreibschweißanlage
- Widerstandsschweißanlagen zum Punkt- und Buckelschweißen
- Ultraschallschweißanlagen
- Gleeble (Anlage zur thermomechanischen, physikalischen Gefügesimulation)
- Div. Universalprüfmaschinen z.B. für Zug, Druck- und Biegeprüfungen
- Mitarbeiter der Abteilung verantworten die Vorlesungen „Fügetechnik“, „Additive Fertigung“ und wirken in weiteren Vorlesungen mit.
- Angebote von experimentellen, numerischen und theoretischen Abschluss- und Studienarbeiten auf unseren Kerngebieten „Fügetechnik“, „Additive Fertigung“ und „Spannungsanalyse“.
- Betreuung von Masterarbeiten in Industrieunternehmen in Absprache bzw. Kooperation mit dem IMWF.
Laserstrahlschmelzen
In diesem Video, welches anlässlich der VDI-Veranstaltung "Wasserstoff - eine Hilfe beim Klimawandel und eine Herausforderung im großtechnischen Einsatz" an der MPA am 27. April 2021 erstellt wurde, erklärt Dr. Martin Werz die Funktionsweise des selektiven Laserschmelzens und die Prüfung der Performance der additiv gefertigten Bauteile unter Wasserstoffatmosphäre.
So finden Sie uns
- Unser Standort auf dem Campus
Pfaffenwaldring 32, 70569 Stuttgart - Open Street Map
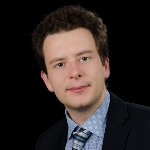
Martin Werz
Dr.-Ing.Abteilungsleiter
- Profil-Seite
- +49 711 685 62597
- E-Mail schreiben
- Abteilung Fügetechnik und Additive Fertigung