Ihr kompetenter Partner für Sicherheitsbewertungen
Wir bieten Ihnen umfassende Beratung bei Fragen zur rechnerischen Analyse und Zustandsbewertung sowohl im Maschinen- und Anlagenbau als auch im Bauwesen. Unsere Dienstleistungen im Maschinen- und Anlagenbau umfassen alle Aspekte von der numerischen Strukturanalyse über die Ermüdungsanalyse bis hin zur bruchmechanischen Bewertung und Zuverlässigkeitsanalyse. Unsere Dienstleistungen im Bauwesen umfassen die Zustandsanalyse von Ingenieurbauwerken. Gerne beraten wir Sie zu Ihrem speziellen Anliegen.
Die Referate der Abteilung Bauteilbewertung und Zuverlässigkeit
-
Bauteilintegrität und Betriebsfestigkeit
Wir bieten Ihnen numerische und analytische Berechnungen zur statischen Festigkeit sowie zur Betriebsfestigkeit von Komponenten im Maschinen- und Anlagenbau. Wir führen unsere Berechnungen sowohl mit kommerziell verfügbaren Finite-Elemente-Programmen als auch mit hauseigenen Berechnungswerkzeugen durch. Zur Bewertung der Betriebsfestigkeit wenden wir aktuelle Normen und Regelwerke an. Unser Tätigkeitsbereich umfasst die isotherme mechanische, thermische und thermo-mechanische Ermüdung
-
Zuverlässigkeitsanalyse und Probabilistik
Wir bieten Ihnen Zuverlässigkeitsanalysen unter Anwendung von probabilistischen Methoden. Wir befassen uns schwerpunktmäßig mit Fragestellungen aus dem Bereich des Lebensdauermanagements von Industrieanlagen (z. B. Kraftwerken, Prozessanlagen). Für Ihre Risikoorientierte Instandhaltung und Inspektionen (Risk Based Maintenance and Inspections) führen wir auf Wunsch auch komplette Risikoanalysen durch und stellen entsprechende Risikomatrizen für Ihre Anlagen auf.
Schwingprüfung
Experimentelle Prüfungen mit zyklischen wechselnden Belastungen an Werkstoffproben und Bauteilen zur Bestimmung von Auslegungs- und Berechnungskennwerten. Zug-, Druck-, Biegebeanspruchungen sowie Torsions- und Innendruckbelastungen können simuliert werden, teilweise können Umgebungseinflüsse wie Temperatur und Korrosion mit berücksichtigt werden. Spannungen und Dehnungen zum Zeitpunkt der Belastungsaufbringung werden genauso ermittelt wie deren zeit- und lastspielabhängiges Umlagerungsverhalten sowie das Schädigungsverhalten (Risseinleitung, Risswachstum).
Aufgaben und fachliche Schwerpunkte
Unsere Abteilung bietet ein umfassendes Spektrum an Dienstleistungen zur rechnerischen Analyse und Zustandsbewertung sowohl im Maschinen- und Anlagenbau als auch im Bauwesen. Informieren Sie sich hier über die von uns angebotenen Leistungen oder kontaktieren Sie uns telefonisch oder per E-Mail.
- Mitarbeit bei Genehmigung und Zulassung von Transport- und Lagerbehältern von abgebrannten Brennelementen
- Zertifizierung nach ISO 9001:2015: „Entwicklung und Support von Datenbanken und Software für Stoffgesetze und Lebensdauermanagement, Steuerung und Regelung in Industrieanlagen“
Eingebunden in unsere Dienstleistungstätigkeiten forschen wir für Sie im Bereich der Bauteilbewertung und Zuverlässigkeit und entwickeln Lösungen zu aktuellen Fragestellungen.
- Numerische Analyse der Fluid-Struktur-Interaktion bei Komponenten des Maschinen- und Anlagenbaus
- Untersuchung des Werkstoff- und Ermüdungsverhaltens von Stahlwerkstoffen im Very High Cycle Fatigue (VHCF)-Bereich
- Untersuchung des Werkstoff- und Ermüdungsverhaltens von Stahlwerkstoffen bei erhöhten Temperaturen unter korrosiven Mediumsbedingungen
- Entwicklung von rechnerischen Bewertungsverfahren für Bauteile mit Mehrfachrissen
- Entwicklung von spezialisierten Softwaremodulen zur Bewertung von metallischen Komponenten bei quasistatischen und zyklischen Beanspruchungen
- Untersuchung von Auswirkungen der Werkstoffparameterunsicherheit auf die Bewertung von Komponenten
- Prüfung von Berechnungsberichten für die maschinentechnische Auslegung von Wasserkraftanlagen
- Begutachtung von Bauteilen des Maschinen- und Anlagenbaus
- Prüfung von Konstruktions- und Fertigungsunterlagen
- Unterstützung bei der Qualitätssicherung in der Fertigung und im Betrieb von Maschinen und Anlagen
- Betreuung von Studierenden (Bachelor-, Studien-, Masterarbeiten) über das IMWF Universität Stuttgart
- Vorlesungen für Studierende über das IMWF Universität Stuttgart
Um unserer gesellschaftlichen Verantwortung gerecht zu werden, beteiligen wir uns aktiv an Fachausschüssen, Gremien und Kommittees und bringen so als unabhängige Stelle wichtige Erkenntnisse aus Forschung, Entwicklung und Anwendung in Richtlinien und Normen ein.
- NEA CSNI WGIAGE (Nuclear Energy Agency - Committee on the Safety of Nuclear Installations – Working Group on Integrity and Ageing of Components and Structures)
- Reaktorsicherheitskommission (RSK) Ausschuss Druckführende Komponenten und Werkstoffe
- DGZfP Fachausschuss Zustandsüberwachung (Structural Health Monitoring)
- Benannte Stelle nach Druckgeräterichtlinie
Flyer der Abteilung
So finden Sie uns
- Unser Standort auf dem Campus
Pfaffenwaldring 32 a, 70569 Stuttgart - Open Street Map
Kontakt
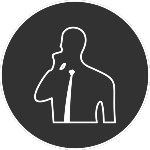
Maximilian Friedrich
M.Sc.Abteilungsleiter / Referatsleiter