Ihr kompetenter Partner
Die Referate der Abteilung Werkstoffverhalten und Werkstoffmodellierung
-
Hochtemperaturwerkstoff- und Hochdruckprüfung
Hochtemperaturwerkstoffprüfung bedeutet, das Werkstoffverhalten unter hohen Temperaturen durch adäquate Experimente darzustellen. In der Regel spielt dort zeitabhängige, inelastische Verformung eine entscheidende Rolle. Diese muss durch hochpräzise Messtechnik ermittelt werden, um als Grundlage für die Anpassung von Werkstoffmodellen und für die Bewertungen nutzbar gemacht zu werden. Dazu gehören Standardversuche unter einachsiger, rein statischer oder zyklischer sowie überlagerter Beanspruchung bei erhöhten Temperaturen. Über Sonderlösungen, die hausintern entwickelt und realisiert werden, können Prüfungen auf Komponentenebene mit komplexen Belastungen aus Kräften, Innendrücken oder Biegemomente durchgeführt werden. Unser erfahrenes Team unterstützt Sie bei Ihrer individuellen Fragestellung umfassend von der Entwicklung des optimalen Mess- und Prüfkonzepts über die praxisgerechte Ausführung bis zur Bewertung der Messdaten.
-
Werkstoffmodellierung
Wir bieten Ihnen an, die in Werkstoffen ablaufenden Prozesse und wirkenden Mechanismen während der Beanspruchung auf mehreren Längenskalen zu untersuchen. Das Verständnis der Wechselwirkung zwischen der Mikrostruktur des Werkstoffs und dem Verformungs- und Schädigungsverhalten ermöglicht eine zuverlässige Abschätzung der Lebensdauer der Bauteile und bildet die Grundlage für "maßgeschneiderte Werkstoffe" mit gewünschten Eigenschaftsprofilen.
-
Hochgeschwindigkeitsbeanspruchung
Das Referat Hochgeschwindigkeitsbeanspruchung untersucht experimentell und numerisch das Werkstoff- und Bauteilverhalten bei erhöhten Beanspruchungsgeschwindigkeiten.
Anwendungsgebiete sind z.B. die Crashsimulation, Sicherheitsanalysen bei schlagartiger Beanspruchung und die Prozesssimulation in der Fertigung.
Wasserstoffeinfluss
Unsere Autoklaven erlauben Werkstoff- und Bauteilprüfungen in Wasserstoffatmosphäre, in Reinstwasser und anderen Medien in einem weiten Temperatur- und Druckbereich. Unsere Mitarbeiter beraten Sie bei der Festlegung von Prüfanforderungen und erarbeiten Lösungen zur Umsetzung komplexer Umgebungsbedingungen im Prüfbetrieb.
Aufgaben und fachliche Schwerpunkte
Unsere Abteilung bietet ein umfassendes Spektrum an Dienstleistungen im Bereich experimentelle Prüfungen und numerischen Berechnungen zum Werkstoffverhalten. Informieren Sie sich hier über die von uns angebotenen Leistungen oder kontaktieren Sie uns telefonisch oder per Email!
- Dynamisches Fließverhalten (z.B. Zugversuch nach DIN EN ISO 26203-2 und SEP 1230)
- Dynamische Bruchmechanik und Schädigungsmechanik (z.B. ASTM E1921)
- Dynamische Bauteilversuche (Fallwerksversuche, Crash)
- Entwicklung, Validierung und Implementierung von geschwindigkeits- und temperaturabhängigen Material- und Schädigungsmodellen unter Berücksichtigung von Mehrachsigkeit und Lodewinkel
- Ermittlung von Materialparametern für empirische und phänomenologische Modelle (Johnson-Cook, Zerilli-Armstrong, Voce, Wierzbicki)
- Numerische Simulation von schlagartigen Vorgängen und Belastungen
- Experimentelle und numerische Simulation von dynamischen Prozessen (Hochgeschwindigkeitsumformen, -zerspanen, -schneiden)
- 2D und 3D FE-Programme zur Modellierung des Verformungs- und Schädigungsverhaltens in idealisierten und realen Gefügetypen
- Molekulardynamik-Simulationsprogramm IMD
- Programm zur 3D Gefügerekonstruktion aus Tomogrammen und Erstellung von Simulationsmodellen
- Schädigungsmechanische Werkstoffmodelle zur Zähbruchbeschreibung (z.B. Rousselier Modell) und Sprödbruchbeschreibung (z.B. Beremin Ansatz)
- Simulations-/netzgenerierungs- und Auswerteprogramme (ABAQUA/CAE,ANSYS,ADINA,PATRAN mit Schnittstellen zu allen gängigen CAD-Systemen
- Zugriff auf Höchstleistungsrechner am Höchstleistungsrechenzentrum Stuttgart (HLRS)
Eingebunden in unsere Industrietätigkeit forschen wir für Sie im Bereich des Werkstoffverhaltens und entwickeln Lösungen zu aktuellen Fragestellungen.
- Molekulardynamik-Simulation zur Analyse der verformungsinduzierten Martensitumwandlung
- Mikrostrukturuntersuchungen und Ableitung relevanter Parameter für die Stoffgesetzentwicklung
- 2D/3D-Modellierung des Werkstoffverhaltens basierend auf mikrostrukturell begründeten Effekten
- Dynamische Bruchmechanik
- Entwicklung von Lösungen zur Umsetzung von Bauteilversuchen bei hohen Temperaturen
- Weiterentwicklung von Werkstoffgesetzen und schädigungsmechanischen Ansätzen
- Weiterentwicklung von Modellen basierend auf FEM
- Kopplung von Prozess-Simulation und Mikrostrukturmechanik
- Untersuchung des Masterkurven-Konzepts bei dynamischer Rissbeanspruchung
- Verformungs- und Versagensverhalten dünnwandiger Rohrleitungen unter Detonationsbeanspruchung
Um unserer gesellschaftlichen Verantwortung gerecht zu werden, beteiligen wir uns aktiv an Fachausschüssen, Gremien und Kommittees und bringen so als unabhängige Stelle wichtige Erkenntnisse aus Forschung, Entwicklung und Anwendung in Richtlinien und Normen ein.
- Prüfstelle in der Forschungsvereinigung Warmfeste Stähle und Hochtemperaturwerkstoffe (FVWHT)
- European-Collaborative-Creep-Committee (ECCC)
- ISO/TC 164 “Mechanical testing of metals”
- ISO/TC 164/SC 01/WG 07 "Tensile testing at high strain rates"
- ISO/TC 164/SC 04 “Toughness Testing”
- ASTM Committee E08 on Fatigue and Fracture
- NA 062 DIN-Normenausschuss Materialprüfung (NMP)
- NA 062-01-42 AA Arbeitsausschuss Zug- und Duktilitätsprüfung für Metalle
- NA 062-01-46 AA Arbeitsausschuss Bruchmechanik
- Großbauteilprüfung bis 2.5 m Länge bis 700°C
- Großprüfmaschinen bis 5 MN
- Korrosionsprüfstand zur Erzeugung Überkritischer Dampfparameter
- Dehnungsgeregelte Innendruckversuche bei Hochtemperatur
- Servohydraulische Schnellzerreißmaschine 100 kN bis 20 m/s
- Temperaturkammer -100°C bis +300°C geeignet für optische Messtechnik
- Split Hopkinson Pressure Bar Anlage
- Fallwerke bis 20kJ / 10 m Fallhöhe
- Hochgeschwindigkeitskameras bis 2 Millionen Bilder pro Sekunde
- DMS-Verstärker bis 1MHz
- Kraftmessglieder für schnelle Vorgänge
Flyer der Abteilung
So finden Sie uns
- Unser Standort auf dem Campus
Pfaffenwaldring 32, 70569 Stuttgart - Open Street Map
Kontakt
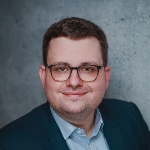
Maximilian Friedrich
M.Sc.Abteilungsleiter / Referatsleiter

Brian Kagay
Dr.Stellvertretender Abteilungsleiter / Referatsleiter