Our team in the "Quality Surveillance and Failure Analysis" unit carries out failure analyses or the review of delivery conditions or material specifications for you on metallic components from the fields of energy, automotive, sanitary engineering or general mechanical and plant engineering. We are specialized in all metallic materials from steel alloys to aluminum alloys to copper alloys of any manufacturing type.
Our service:
Send us your specific request. We will then draw up an MPA-wide, results-oriented investigation program and report our findings on an ongoing basis to you. Finally, you will receive an investigation report with result interpretation and target-oriented recommendations.
Tasks and main focus
- Macro- and microscopic damage analysis
- Macro- and microfractography by stereo microscope and SEM
- Metallography
- Wear investigations
- Investigation of coatings
- Planning and interpretation of residual stress analyses
- Viewing of technological documents e.g. with regard to the cause of damage
- Review of material specifications
- Examination of older construction materials with regard to their further use
- Tensile and compression tests according to standards and individual specifications
- Pendulum impact test
- Bend tests
- Component tests
- Universal testing machine: static, rapid up to 580 mm/min from 200 N to 300 kN (tension, compression, bending) with a temperature chamber (temperature range: - 150 °C < T < 300 °C)
- High-resolution extensometer measuring on both sides for E-modulus determination
- Pendulum impact tester up to 300 J with temperature chamber (- 150 °C to 500 °C)
- Pendulum impact tester up to 15 J for testing very small specimens
- Optical correlation measuring system (DIC) for individual testing tasks
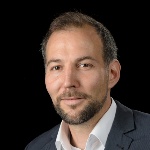
David von Mirbach
Dr.-Ing.Deputy Head of Department / Head of Unit

Rahel Eisele
Dr. rer. nat.Head of Unit / Deputy Head of Unit